L’Associazione Sportiva Velate Rugby 1981 è stata istituita nel comune di Usmate-Velate (in provincia di Monza e Brianza) nel 1981 e dalla data di fondazione a oggi è sempre stata caratterizzata per la capacità di raccogliere intorno a sé molti ragazzi e tantissime famiglie. Questo spirito di aggregazione è stata la forza motivazionale che ha spinto i dirigenti della società a decidere di dare una nuova casa al gruppo.
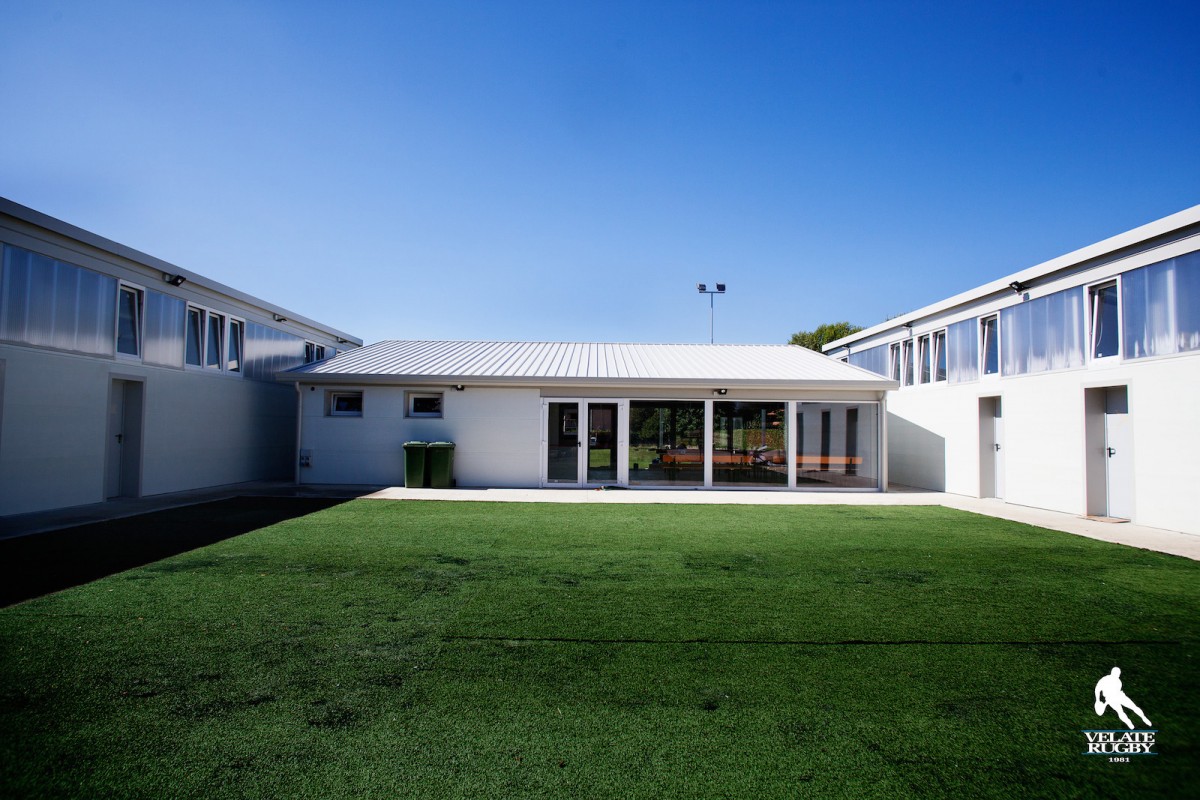
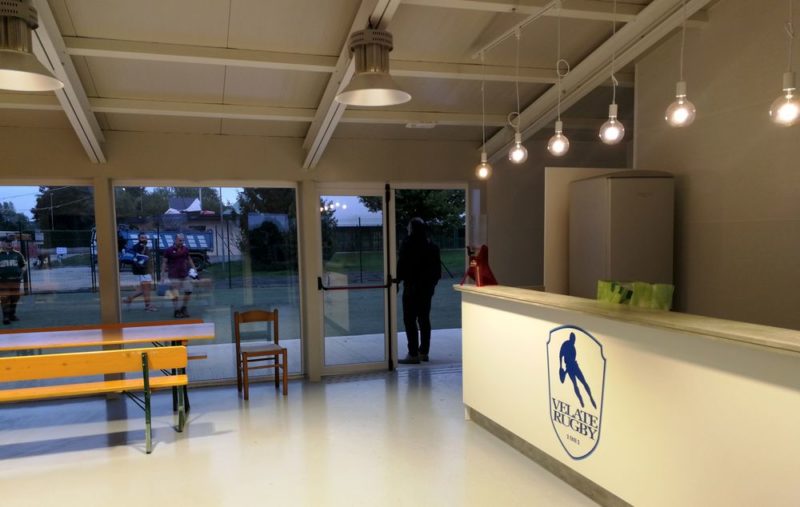
Esterni e interno a lavori ultimati.
I tre padiglioni del nuovo mini campus
Il progetto della nuova sede è stato quindi concepito come un mini-campus costituito da tre padiglioni distinti che formano una corte centrale edificata sui tre lati; il quarto lato, volutamente mancante, costituisce l’accesso principale per i giovani atleti, le famiglie, i tifosi e i visitatori.
L’edificio cosi configurato si pone come filtro tra il restante centro sportivo comunale (posto alle sue spalle) e il campo di rugby che si svela approcciandosi alla corte. L’edificio della Club House è collocato al centro della composizione architettonica e con le sue ampie vetrate consente di visualizzare e valorizzare il campo da gioco dando vita a una continuità percettiva tra la corte e il campo stesso, all’interno trovano spazio una sala destinata ai momenti di condivisione e ristorazione, affiancati da un’ampia cucina.
Le ali della corte sono destinate agli spogliatoi della squadra di casa e degli ospiti, agli spogliatoi per arbitri, all’infermeria, all’ufficio e ai magazzini. Un ruolo importante nella lettura dei volumi dei tre edifici è stato assegnato alla forma della copertura, una falda unica che caratterizza i singoli manufatti che parte da un’altezza minima di 260 cm fino ad arrivare ad una quota di 420 cm; in questo modo la semplicità costruttiva si è coniugata con un disegno deciso e minimale consentendo di concentrare e ordinare le finestre in un’unica fascia orizzontale all’interno della quale si alternano le trasparenze del vetro e le specchiature traslucide dei pannelli in policarbonato.Le grandi aperture finestrate rivolte verso la corte dei due edifici laterali destinati a spogliatoio, garantiscono agli spazi interni di godere di una buona luminosità diretta e indiretta in tutte le ore del giorno; verso l’esterno del complesso le aperture sono invece state ridotte al minimo esclusivamente per consentire un adeguato riscontro d’aria e generare una ventilazione incrociata per raffrescare in modo naturale l’edificio. A illustrare la nuova realizzazione come spazio di aggregazione sono stati l’arch. Enrico Gastaroba e gli ingegneri Emanuele della Torre.
IL CANTIERE SMART
Anche la fase di cantierizzazione, come la progettazione, ha richiesto un importante lavoro di affinamento legato agli aspetti di sicurezza, logistica e soprattutto di economicità.Era infatti imperativo che non vi fossero aggravi di costi legati a possibili varianti in opera, anche minori, in quanto le riserve di economia non avrebbero potuto coprire nuove lavorazioni o opere accessorie non previste.
L’allestimento di cantiere è stato ridotto al minimo: la delimitazione dell’area di cantiere è stata realizzata con reti metalliche recuperate da altri cantieri in fase di smobilitazione; per i servizi igienici è stata utilizzata una convenzione con il locale ristori del centro poli-sportivo; l’ufficio di cantiere è stato ricavato in una prima fase in container provvisori isolati e condizionati e in seconda fase all’interno degli stessi locali in allestimento.
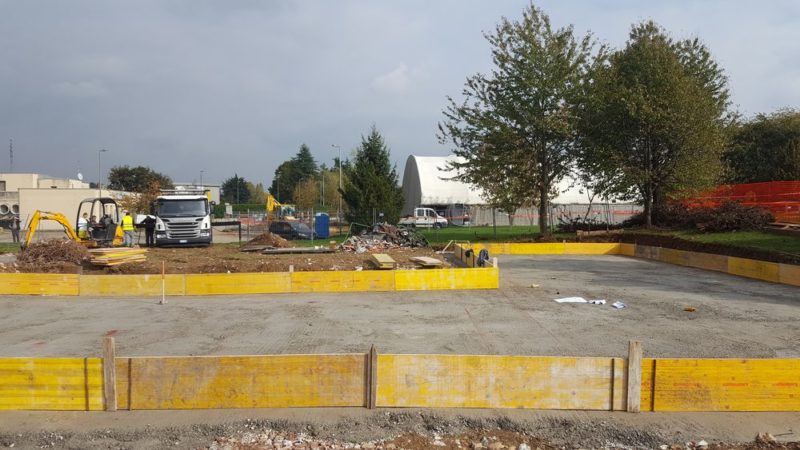
Scavi e sbancamento ridotti al minimo
Nell’area esisteva infatti un piccolo baraccamento in muratura di laterizio che è stato demolito solo nella porzione fuori-terra. Una volta effettuato lo scoticamento, lo scavo di sbancamento generale è stato impostato a una quota di poco inferiore al metro di profondità.
Le fondazioni e i muri contro-terra del piccolo fabbricato demolito sono state riempite con materiale drenante e compattato proveniente dalla demolizione dello stesso fabbricato. La posa del magrone con rete elettrosaldata e un getto aggiuntivo di calcestruzzo fluidificato, ha consentito di evitare lo scavo ulteriore che si sarebbe dovuto altresì realizzare per rimuovere le fondazioni del vecchio fabbricato, mantenendo la quota minima del piano d’imposta della nuova costruzione.
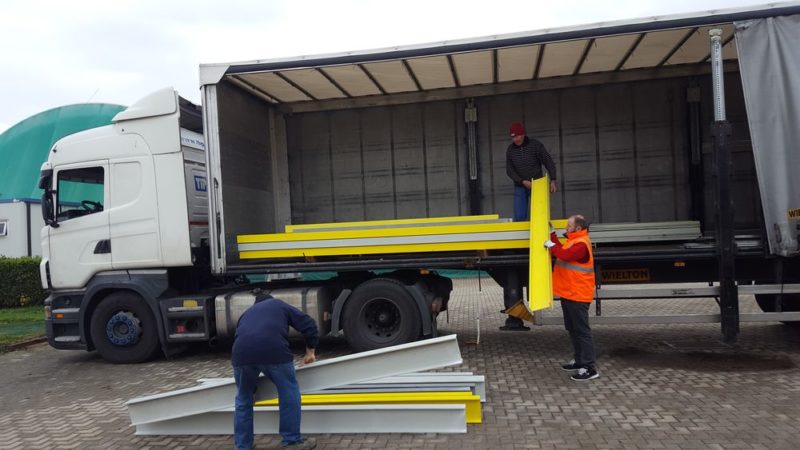
Fondazioni
Sul piano di fondazione sono state posate le armature della platea nervata, in particolare le gabbie delle travi di armatura sono state prodotte in officine specializzate in base ai disegni esecutivi; le armature delle altre porzioni di platea (aventi maglia regolare sia nelle armature superiori che inferiori) sono invece state realizzate in opera a partire da reti elettrosaldate sormontate fra loro.
Una difficoltà operativa è stata riscontrata nel livellamento delle travi di fondazione che erano destinate ad accogliere le piastre in acciaio con le barre di ancoraggio dei pilastri in vetroresina.
Per recuperare il perfetto livellamento è stato fatto effettuare in officina un taglio di regolazione a 45° nelle piastre, fissato poi in opera, a regolazione avvenute, con saldature di bloccaggio sulle medesime piastre. Una volta riprese le piastre con passivizzante per evitare possibili fenomeni di deterioramento, è stato possibile inserire i pilastri in vetroresina ed effettuare il riempimento con malta antiritiro fra piastre e travi.
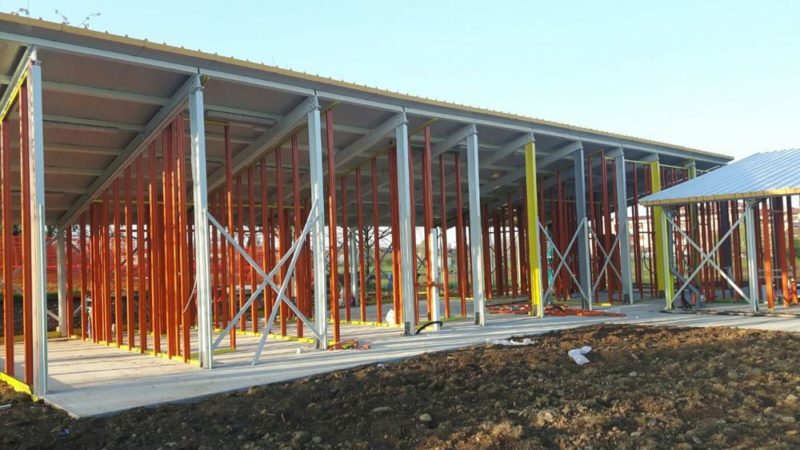
Pilastri in vetroresina
L’operazione di verticalizzazione dei pilastri è stata resa molto agevolata dal peso esiguo dei pilastri in vetroresina che hanno reso possibile la movimentazione manuale da parte di due persone solamente.
I pilastri nella parte sommitale sono stati tagliati con lama ad acqua nell’officina di produzione, tale taglio ha permesso di eliminare le due ali del profilo (profilo Hea 200) nella porzione d’innesto delle due travi C200, costituenti l’orditura del tetto e fissate di schienacon bulloneria in acciaio direttamente sull’anima del pilastro.
La modalità di fissaggio utilizzata rende libera la regolazione della pendenza delle travi di copertura permettendo un perfetto posizionamento e livellamento di tutti i telai che sono andati a realizzare la struttura tipica ad anello dell’intervento.
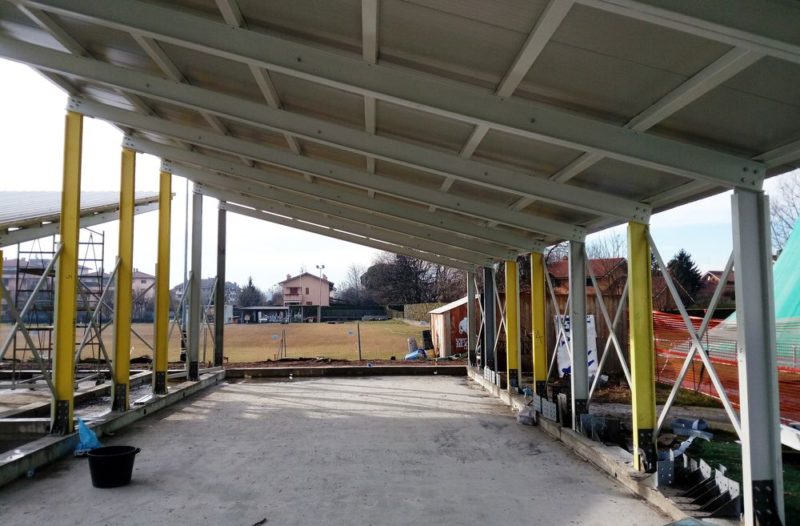
Copertura e controventature
Il tetto, in pannelli sandwich pre-coibentati, è stato posato una volta completata tutta la struttura ad anello dei 3 corpi di fabbrica e costituita da serie ripetuta di telai trapezoidali in vetroresina. Unitamente alla copertura sono state montate le controventature anch’esse in vetroresina e agenti nel piano ortogonale a quello dei telai ad anello.
Il fissaggio di questi elementi (tubolari quadri a sezione cava) è avvenuto con viti auto-filettanti all’interno delle ali dei pilastri in vetroresina. La corretta sequenza di posa di telai e controventi ha consentito di evitare pose aggiuntive di schermi antiventonecessari per evitare l’effetto vela della copertura, nell’arco temporale in cui le pareti perimetrali non erano ancora state montate.
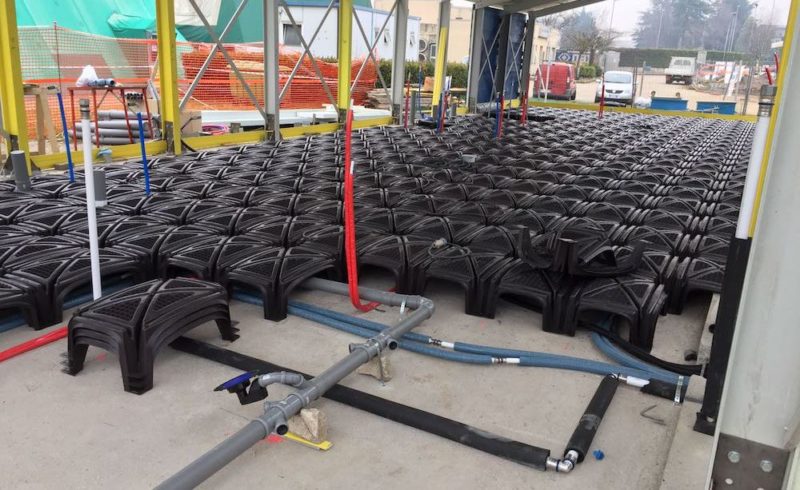
Posa degli impianti
Concluso il montaggio della copertura e delle strutture principali è iniziata la posa degli impianti idrici ed elettrici con anche l’allestimento della centrale termica: della caldaia a condensazione e dei grandi serbatoi di accumulo, operanti con i collettori solari, necessari per gestire in modo razionale tutte le docce degli spogliatoi e in generale tutta la produzione di acqua calda sanitaria.
Per le linee idriche sono state utilizzate tubazioni in polipropilene multistrato pre-isolate e dotate di barriera anti-ossigeno. La giunzione delle linee impianti è pertanto stata effettuata con un numero di punti di collegamento molto ridotto tramite innesti a tenuta meccanica di rapida esecuzione e a garanzia di una perfetta tenuta nel tempo.
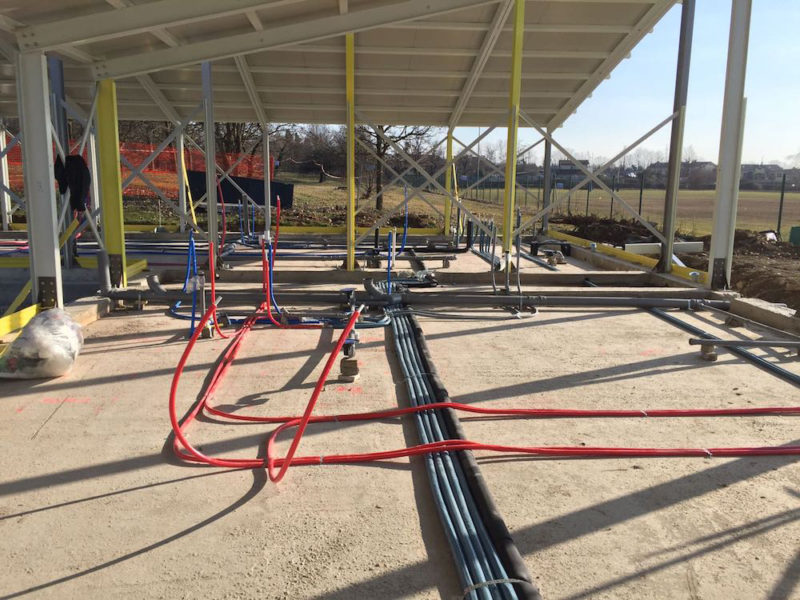
Interni e facciate esterne
Una volta effettuate tutte le predisposizioni impiantistiche a pavimento è stato effettuato un massetto di ricopertura con fibre anti-ritiro studiato specificatamente per ricevere la successiva finitura in resina cementizia antiusura e antisdrucciolo.
Questa finitura in particolare è stata scelta per le sue caratteristiche d’impermeabilità che la rendono idonea all’utilizzo in locali umidi, quali ad esempio le docce, ma è stata estesa per uniformità e a garanzia di maggior resistenza nel tempo in tutti gli altri ambienti del complesso.
Completato il massetto è iniziato il montaggio sia delle pareti interne a secco, con profili e lastre in vetroresina, sia il montaggio delle facciate esterne con gli speciali profili strutturali sagomati per accogliere le lastre nervate di tamponamento anch’esse in vetroresina pultrusa.
Per scelta di carattere estetico-formale si è preferito lasciare al naturale le sopra-citate lastre di chiusura in modo da consentire una buona superficie di aggrappo per la vernice a smalto per esterni di finitura ove prevista o del protettivo lucido trasparente.
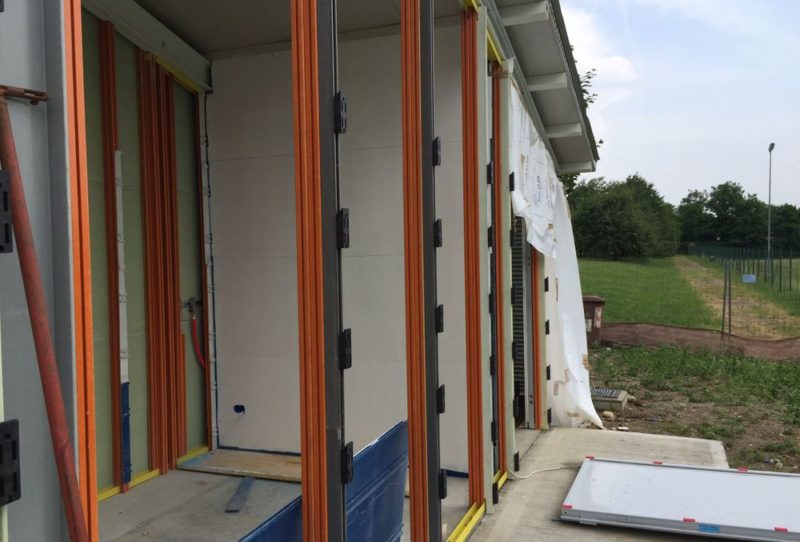
Isolamento delle tamponature
Completata la «pelle» esterna in Vtr, massima attenzione è stata data nella posa degli isolanti delle tamponature sugli ambienti freddi. Direttamente sulla faccia interna della pelle di facciata sono stati quindi posizionati: prima un pannellatura in Eps battentato a formare uno strato omogeneo ripreso nei punti di sfrido con schiuma poliuretanica per evitare ogni possibile trafilamento d’aria; poi uno strato di lana di roccia a fibre lunghe, bio-compatibili e impregnate con leganti a base di olii minerali per evitare la possibile dispersione di polveri dovute al taglio dei pannelli, aventi la funzione di garantire l’assorbimento acustico dell’intercapedine e quindi il corretto isolamento acustico della facciate; infine è stata posata la lastra di finitura interna anch’essa in Vtr.
Tutta la stratigrafia risultante è stata sottoposta a controlli in opera e ispezioni a campione anche tramite termografie atte all’eliminazione di ogni possibile ponte termico. Ove previsti prima della chiusura della lastra interna in Vtr sono stati posizionati i serramenti in pvc con vetrocamera in argon e trattamento dei vetri per renderli basso emissivi e schermanti alla radiazione solare.
Durante queste fasi intermedie sono stati ultimati anche gli impianti d’illuminazione interna, in particolare quello della sala comune con i grandi lampadari a Led di design industriale e quello dell’illuminazione esterna, realizzata con fari a Led IP 65 fissati direttamente sulle lastre in Vtr della facciata.
Particolare attenzione è stata riservata al posizionamento del sistema di video-sorveglianza realizzato con telecamere infrarosse e collegate alla rete dati del complesso. In ultimo sono state completate le pavimentazioni esterne, è stato livellato e seminato il nuovo manto erboso del campo da rugby ed è stata posata la pavimentazione in erba sintetica di recupero della corte interna.
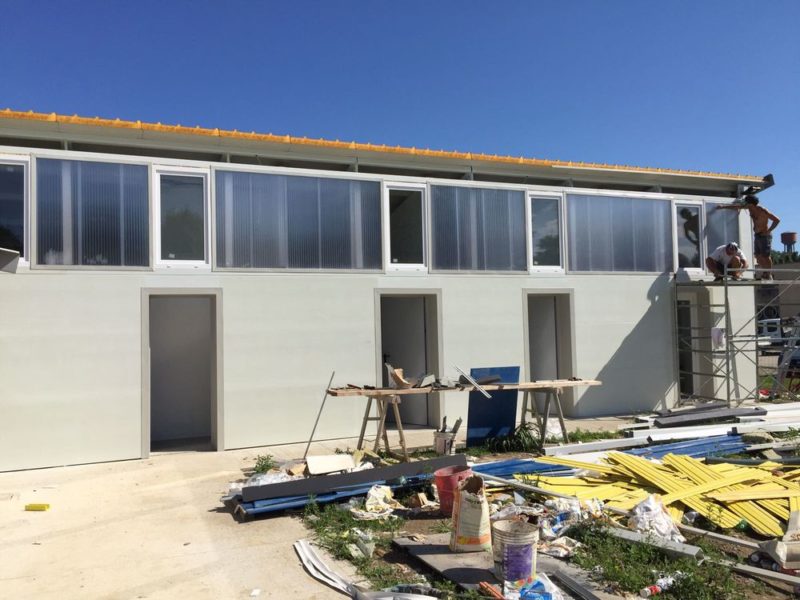
Innovazione: i materiali polimerici fibrorinforzati
Nel settore delle nuove costruzioni assistiamo a interessanti sperimentazioni per lo più ispirate dalla prefabbricazione di tipo «leggero» e «aperto», che consente l’assemblaggio – su una vasta gamma modulare e in modo flessibile – di componenti realizzati in officina, già dotati di elevati contenuti prestazionali. La separazione netta degli elementi strutturali da quelli tecnici e la progettazione di quest’ultimi come assemblaggio di componenti altamente specializzati apportano notevoli vantaggi ambientali al processo edilizio in termini di:
- diminuzione di peso e aumento dell’efficienza prestazionale degli edifici (grazie alla combinazione sinergica di materiali leggeri che assolvono determinate funzioni);
- riduzione di tempi, costi e consumi delle lavorazioni in officina e in cantiere (attraverso lo sviluppo delle fasi di montaggio a secco dei componenti);
- contrazione dei consumi energetici degli edifici in fase di esercizio (grazie a una più attenta progettazione del sistema involucro/impianti e all’impiego di fonti energetiche rinnovabili).
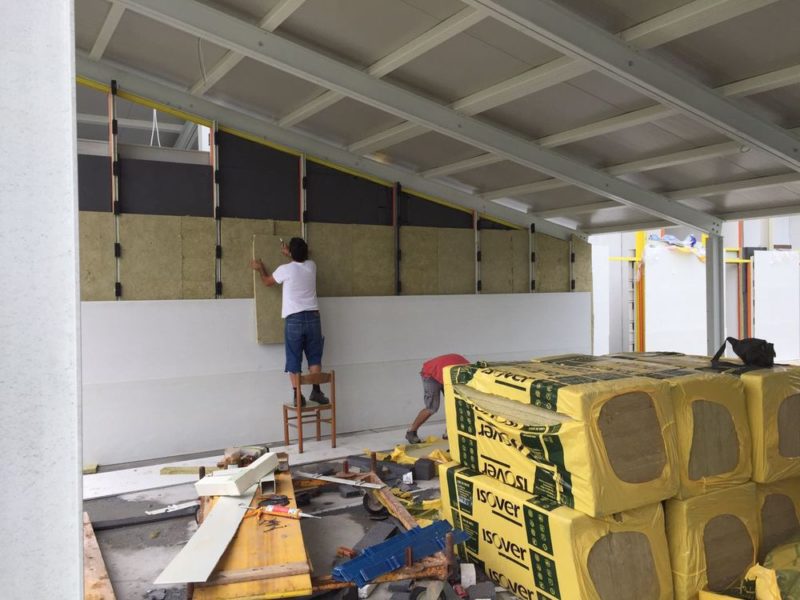
La strada verso i processi d’industrializzazione del processo edilizio, realmente sostenibili sotto il profilo ambientale, appare lunga e complessa. A parziali aperture verso l’uso di materiali innovativi non fa seguito l’attivazione di nuovi processi industriali o la diffusione di nuove tecnologie.
Per risultare efficace e diffondibile su ampia scala l’innovazione dovrà interessare tanto i materiali quanto i sistemi costruttivi nell’ottica di una massimizzazione dei risultati già parzialmente conseguiti nel campo della sostenibilità ambientale del processo edilizio. I materiali polimerici fibrorinforzati, e in particolar modo i pultrusi, risultano avere un elevato potenziale in ambito edilizio.
I prodotti pultrusi vengono oggi ampiamente utilizzati in diversi settori in campo industriale e chimico, tuttavia, la flessibilità della tecnologia, la totale riciclabilità della materia prima e le prestazioni dei prodotti pultrusi ne fanno materiali ideali per la realizzazione di oggetti edilizi di nuova generazione.
Nel settore delle nuove costruzioni i manufatti pultrusi, soprattutto in vetroresina, hanno già trovato applicazioni nella realizzazione di opere di finitura come infissi (in sostituzione dell’acciaio e dell’alluminio) o pannelli leggeri autoportanti per il tamponamento di opere prefabbricate, oppure facciate ventilate (si veda Hotel Sheraton di Malpensa).
Dall’analisi condotta, si evince che, sotto il profilo del bilancio ambientale, i materiali pultrusi fibrorinforzati riducono le risorse utilizzate nel processo costruttivo e sono disponibili a nuove fasi di riutilizzo e riciclaggio: il loro impatto ambientale è del tutto paragonabile al legno e significativamente meno impattante rispetto al calcestruzzo armato (si veda la tabella con i dati del Cnr Messina).
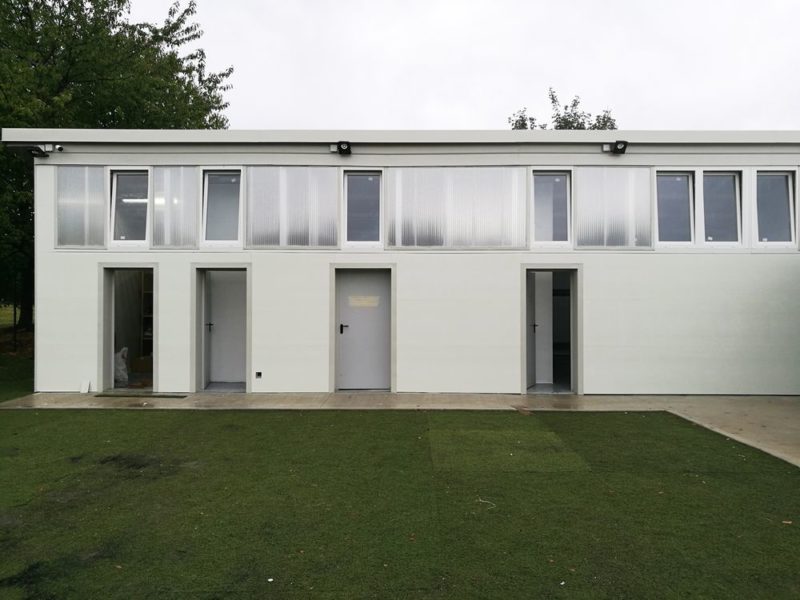
cof
L’integrazione di struttura, involucro e impianti
Il progetto di costruzione degli spogliati ha cercato d’integrare tre componenti autonome: la struttura, l’involucro, gli impianti conseguendo i seguenti obiettivi primari:
- il raggiungimento delle massime prestazioni strutturali ed energetiche del sistema struttura/involucro attraverso l’integrazione tecnologica della fibra di vetro e degli isolanti;
- l’integrazione completa degli impianti elettrici e meccanici con il sistema struttura/involucro all’interno degli stessi nei pannelli in fibra di vetro;
- l’approvvigionamento locale dell’energia da fonti rinnovabili e l’eventuale cessione alla rete delle quote in eccesso.
Il progetto si applica alla tecnologia industriale per la prefabbricazione in fibra di vetro (materiale composito per struttura e involucro). La pultrusione è un processo in continuo per la produzione di profili in termoindurente rinforzati con fibra di vetro: un’estrusione cha avviene grazie al tiro delle fibre impregnate di resina (vedi foto).
Generalmente la pultrusione viene effettuata con rinforzo di fibre di vetro e/o di carbonio e una matrice a base di resina. I prodotti pultrusi sono in grado di garantire livelli ottimali di resistenza meccanica (50 Kg/mm2 a trazione, 25.000 Mpa modulo elastico), resistenza al fuoco, opacità dei fumi in caso d’incendio, isolamento elettrico e termico, resistenza chimica, resistenza agli UV oltre a bassissimi indici di dilatazione termica ed estrema leggerezza. Il materiale pultruso (anche con diversi livelli e strati di finitura) è stato utilizzato in tutte le componenti della struttura e dell’involucro.
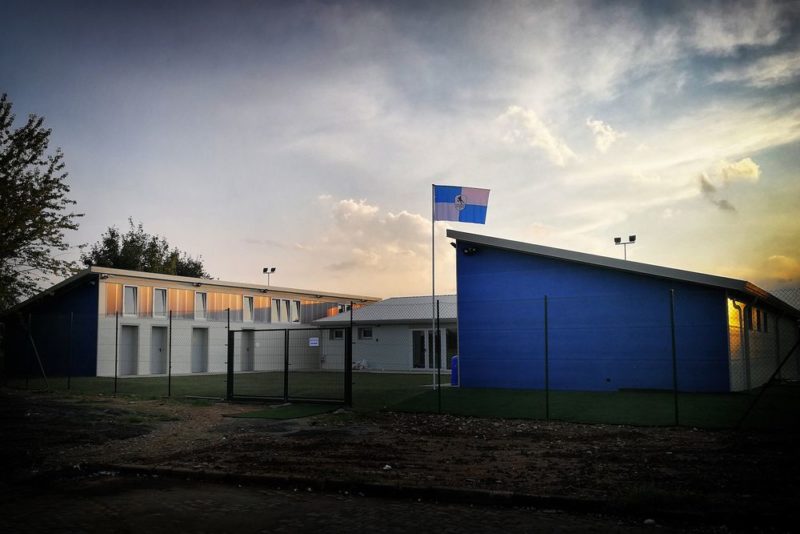
sdr
Ampiamente utilizzati nel settore chimico, i prodotti pultrusi non hanno ancora avuto la giusta introduzione nel settore edilizio per le rigidità del mercato di riferimento, per la scarsità di mano d’opera specializzata e per i costi di progettazione e produzione elevati.
Il progetto ha inteso superare questi ostacoli puntando sullo sviluppo di un oggetto edilizio caratterizzato da una matrice tecnologica prevalente in grado di penetrare il mercato con significative economie di scala. La flessibilità della tecnologia, la totale riciclabilità della materia prima e le prestazioni dei prodotti pultrusi ne fanno infatti materiali ideali per la
realizzazione di oggetti edilizi di nuova generazione.
Arch. Enrico Guastaroba | Il progetto
Il progetto della nuova sede è stato concepito come un mini-campus costituito da tre padiglioni distinti che formano una corte centrale edificata sui tre lati; il quarto lato, volutamente mancante, costituisce l’accesso principale per i giovani atleti, le famiglie, i tifosi e i visitatori. L’edificio cosi configurato si pone come filtro tra il restante centro sportivo comunale -posto alle sue spalle – e il campo di rugby che si svela approcciandosi alla corte.
Ing. Emanuele Della Torre | Il cantiere
Anche la fase di cantierizzazione, come la progettazione, ha richiesto un importante lavoro di affinamento legato agli aspetti di sicurezza, logistica e soprattutto di economicità. Era infatti imperativo che non vi fossero aggravi di costi legati a possibili varianti in opera, anche minori, in quanto le riserve di economia non avrebbero potuto coprire nuove lavorazioni o opere accessorie non previste.
Luca Panzeri | Materiali e sistemi costruttivi innovativi
Nel settore delle nuove costruzioni assistiamo a interessanti sperimentazioni per lo più ispirate dalla prefabbricazione di tipo «leggero» e «aperto», che consente l’assemblaggio – su una vasta gamma modulare e in modo flessibile – di componenti realizzati in officina, già dotati di elevati contenuti prestazionali. La separazione netta degli elementi strutturali da quelli tecnici e la progettazione di quest’ultimi come assemblaggio di componenti altamente specializzati apportano notevoli vantaggi ambientali al processo edilizio.
Chi ha fatto Cosa
Progetto architettonico: arch. Enrico Guastaroba
Progetto e direzione lavori: ing. Luca Panzeri
Progetto strutturale: ing. Emanuele Della Torre
Progetto acustico: Biobyte srl
Progetto termotecnico: Mh contract srl
Progetto impianti elettrici: Mh contract srl
Impresa edile: Interedil di Ruggeri Gigi
Impresa movimento terra: Interedil di Ruggeri Gigi
Montaggio strutture: Interedil di Ruggeri Gigi
Strutture e pannelli rivestimento interni ed esterni in vetroresina: Fibrenet srl
Copertura tetto: Csd Specialisti del Tetto
Serramenti: Uninfissi srl
Fornitura caldaia: Immergas
Sanitari: Colombo Idro spa
Idraulico: Colombro Idro spa
Recinzione: Reti Rusconi srl
Guarda tutte le immagini